Some Examples Of Tools Options

Spool Bore Holes
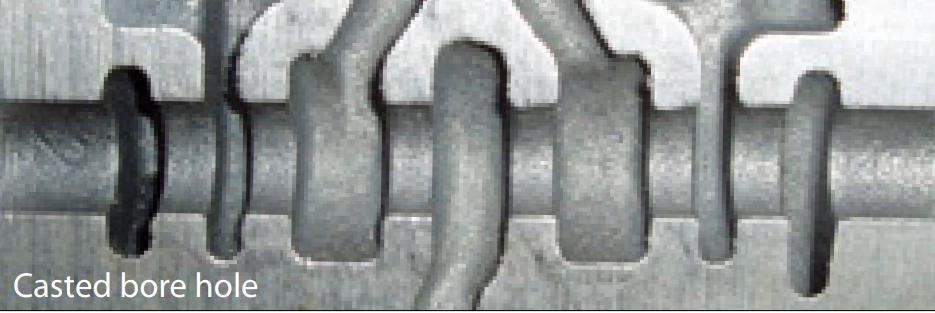
Objective
To eliminate rings produced in the bore by the rough pass reamer. In the typical process these rings need to be removed manually prior to finishing/assembly.
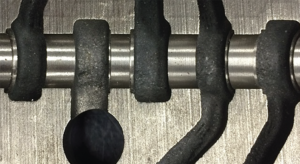
Result
Excellent size consistency
A straight hole free of rings
Huge cycle-time reduction (50%)
15 minutes saved per part
Machining Process
Pilot Drill

Article no. 212851/999999 n = 2000 rpm fn = 0.4 mm/rev.
Ring-free reamer

Article no. 212891/999999 n = 1415 rpm fn = 0.25 mm/rev.
Grooving Land

Article no. 432355/999999 n = 1990 rpm fn = 0.06 mm/rev.
Oil Holes
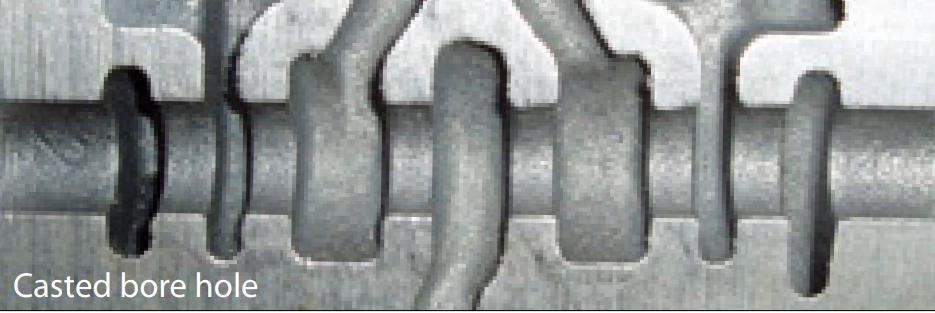
Objective
To reduce the often very long machining time of the deep holes in small diameters with no diameter tolerance (in oil connection holes). In many cases, hss deep hole drills are still used.
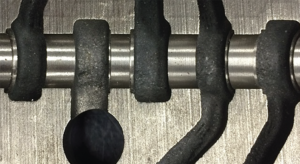
Result
Solid carbide drills with c7 PLUS™ coating ensures increased speed and feed and reduce the cycle time considerably while giving increased life time. Very narrow hole tolerances and a completely safe proces.
Machining Process
Pilot Drill

Article no. 289411.0400> n = 9550 rpm fn = 0.2 mm/rev.
SC deep hole drill

n = 6000 rpm fn = 0.3 mm/rev.
Cavity Holes
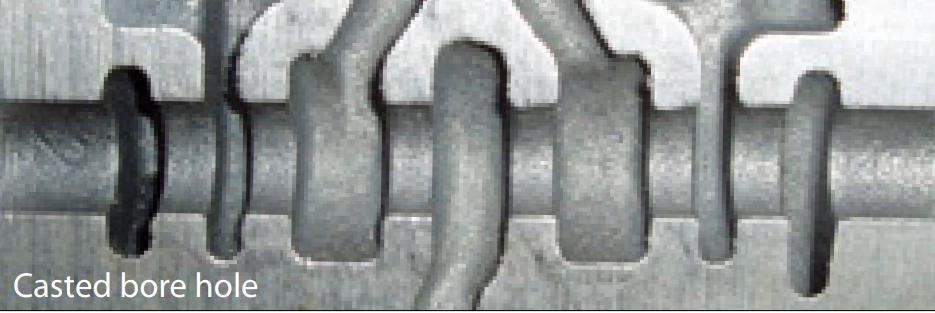
Objective
To reduce the number of tools needed by combining more operations in one. Machine without vibration to obtain narrow diameter tolerance and perfect surface roughness.
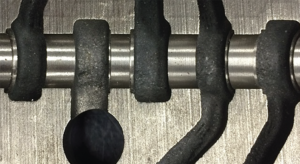
Result
Reinforced core diameter and extra guide pads on the solid carbide drills with helix perform extremely well.
Reduced machining time
No vibration
Safe process
Surface quality: ra 0.8
Hole tolerance: H7-H8
A straight hole
Machining Process
Predrill, standard or customised

Article no. 212890/999999 n = 1530 rpm fn = 0.5 mm/rev.
Core drill

Article no. 212120/999999 n = 1075 rpm fn = 0.4 mm/rev.
Core drill

Article no. 212891/999998 n = 1911 rpm fn = 0.3 mm/rev.
Core drill
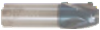
Article no. 212120/999998 n = 1911 rpm fn = 0.3 mm/rev.
Shock Valve Holes
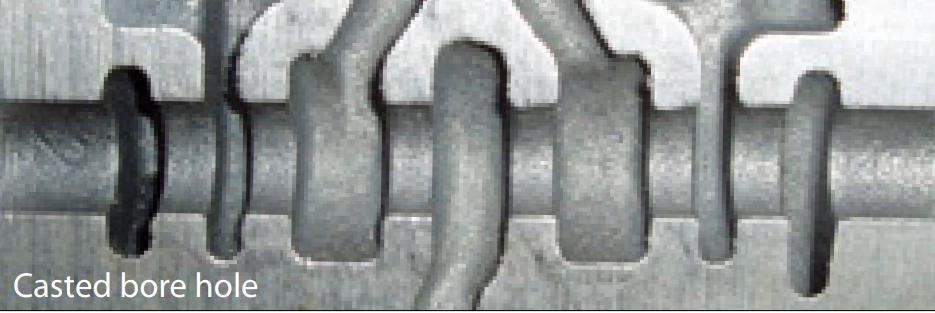
Objective
A fast and reliable process ensuring that the tolerances are achieved in the most efficient way. a typical challenge is to meet the demands for a good surface quality.
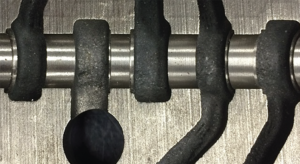
Result
One shot drill with extra guide pads and c7 PLUS™ coating creating a straight hole with excellent surface quality while maintain- ing high feed and a long tool life. The c3 coated thread milling cutter ensures a reliable threading process.
Machining Process
SC step drill

Article no. 12861/999989 n = 1794 rpm fn = 0.35 mm/rev.
Thread milling cutter

Article no. 256910.12x150
Compensator Holes
Objective
To reduce the often long machining time while achieving a high degree of size consistency. To eliminate rings in the bore, produced by the rough pass reamer, that are often stuck in the component and need to be removed manually.
Result
The new process strategy and technology replace straight fluted tools with helix tools to eliminate the problem with rings. The reinforced core diameter and extra guide pads give a straight hole with excellent size consistency. in addition, the cycle time is often reduced by more than 50%.
Machining Process
SC twist drill

Article no. 289412.1200 n = 3881 rpm fn = 0.25 mm/rev.
SC core drill

Article no. 212891/999999 n = 2000 rpm fn = 0.4 mm/rev.
SC Ring-free reamer

Article no. 212851/999999 n = 1415 rpm fn = 0.25 mm/rev.
SC drill

Article no. 212120/999997 n = 2158 rpm fn = 0.35 mm/rev
Port Holes
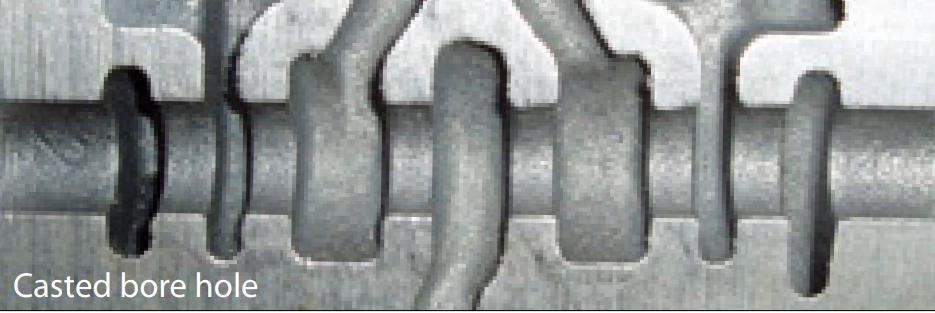
Objective
The large diameter must be created in a drilling operation. must be machined without vibration to obtain narrow diameter toler- ances and perfect surface roughness.
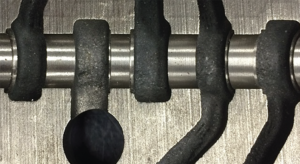
Result
The step drill in pre-form carbide with special internal cool- ant and centre point makes it possible to increase cutting speed.
Reduced machining time
No vibration
Safe process
Excellent surface quality
Long tool life
Machining Process
SC step drill
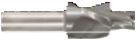
Article no. 212891/999997 n = 1675 rpm fn = 0.4 mm/rev.
UM tap

Article no. eH1480.554
UM thread mill

Article no. 256938.12×014
Relief Valve Holes
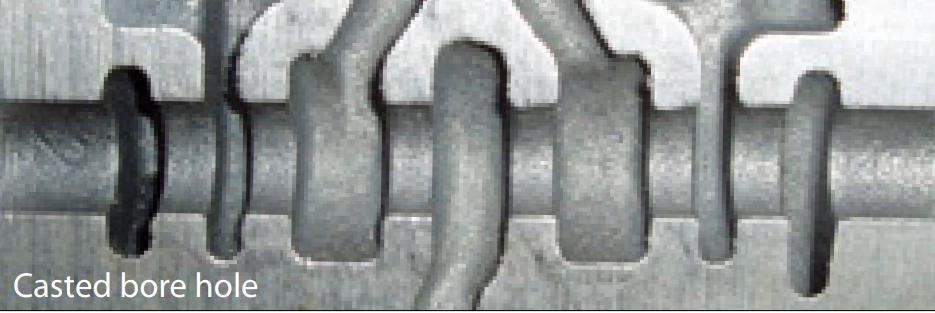
Objective
To create a straight hole meeting high tolerance and surface demands. Reduce the machining time while keeping a reliable process.
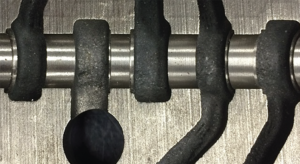
Result
The process strategy with a solid carbide step drill and step ream- er reduce the process time and produce a straight hole with tight tolerances and an excellent surface finish. Due to the c7 PLUS™ coating, tool life time is prolonged considerably.
Machining Process
SC step drill

Article no. 252742/999997 n = 2580 rpm fn = 0.22 mm/rev.
Step reamer

Article no. 212850/999999 n = 2546 rpm fn = 0.35 mm/rev.
HSS tap

Article no. en1270096
Email id
sales@murthyindustries.com
Contact No.
+91-9878986545
Address
#616 , 14th Cross,15th Main, Sector-4, HSR Layout Bangalore-560102